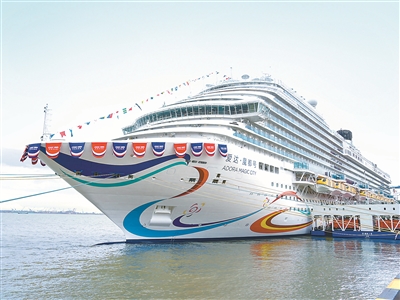
11月4日,我國國產首艘大型郵輪“愛達·魔都號”正式命名交付。圖為當日拍攝的“愛達·魔都號”郵輪。 新華社記者 丁汀 攝
11月4日,國產首艘大型郵輪正式命名交付。作為高技術、高附加值船舶產品,它填補了中國造船“拼圖”上的最后一塊空白,標志我國全部摘取航母、大型液化天然氣船、大型郵輪三顆造船業(yè)“皇冠上的明珠”。
前三季度,我國造船完工量、新承接船舶訂單量、手持船舶訂單量三大指標均保持兩位數(shù)增長,以載重噸計分別占全球總量的48.7%、68.5%和54.7%,以修正總噸計分別占46.0%、63.5%和50.2%,均位居世界第一。
黨的二十大報告提出,推動制造業(yè)高端化、智能化、綠色化發(fā)展。作為裝備制造業(yè)的重要部分,船舶工業(yè)如何實現(xiàn)高端化、智能化、綠色化?從造船大國駛向造船強國,中國巨輪如何乘風破浪?記者采訪了相關企業(yè)和專家。
我國造船業(yè)向高端制造邁進,一批高技術、高附加值船舶相繼完工交付
廣州南沙龍穴島,塔吊林立,機器轟鳴,汽車運輸船、集裝箱船、半潛船等多型船舶同時建造,在碼頭岸邊一字排開。
P&O1500客/3658米車道豪華客滾船2號船是其中之一。這是全球首型大容量電池混合動力豪華客滾船,由中國船舶集團廣船國際公司(以下稱“廣船國際”)為英國P&O Ferries公司建造,即將投入到英吉利海峽運營,往返于英國多佛港和法國加來港。
“今年2月我們交付了首制船,眼前這艘是它的姊妹船,可同時搭載1500名乘客和700多輛各類型車輛。”廖明是這艘船的建造總指揮,他讓記者留意船頭和船艉——長得幾乎一模一樣。
“這艘船的艏艉各有一個駕駛室,內置同款操作設備,因此可以實現(xiàn)艏艉雙向航行,無需調頭,有效縮短進出港時間,提高運營效率。”廖明說,在國際上,在大型客滾船中采用這種雙頭設計尚屬首例。
豪華客滾船屬于高端船型,是廣船國際目前承接的主要船型之一。“目前公司手持造船訂單70余艘,價值超過500億元,高技術、高附加值產品占比超過90%,訂單排期已到2027年。”廣船國際副總經理周旭輝說。
全球造船行業(yè)正處于一個新的復蘇周期。隨著老船淘汰更新、環(huán)保新規(guī)落地,國際市場新船需求旺盛。我國造船企業(yè)主動出擊,憑借實力搶抓訂單,開足馬力加緊生產。據(jù)中國船舶工業(yè)行業(yè)協(xié)會發(fā)布,2023年三季度中國造船產能利用監(jiān)測指數(shù)(CCI)878點,比去年同期提高161點,同比增長22.5%,創(chuàng)近年來新高。具體來看,三季度我國船舶新接訂單量繼續(xù)保持較高水平,同比增長96.9%,帶動手持訂單量環(huán)比增長8.2%。重點監(jiān)測造船企業(yè)手持訂單充足,生產任務飽滿,產能利用保持較高水平。
低端產能過剩、高端產能不足,曾一度是中國船舶工業(yè)的主要困境。如今,我國造船業(yè)結構不斷調整,正向高端制造邁進,一批高技術、高附加值船舶相繼完工交付。
6萬張圖紙、4年多時間、將近2280萬設計與建造工時……一系列數(shù)字,記錄了國產大型郵輪從一塊焊接鋼板到一座“海上城市”的歷程。
“自2019年10月開工點火以來,我們先后攻克了郵輪重量控制、振動噪聲、安全返港等關鍵設計技術,打破了只有歐洲才能建造大型郵輪的格局。”中國船舶集團上海外高橋造船公司(以下稱“外高橋造船”)總經理陳剛說。
“我國船舶工業(yè)的船型研發(fā)與設計能力顯著提升,已經具備承接世界所有主力船型的能力。”中國船舶工業(yè)行業(yè)協(xié)會秘書長李彥慶說,去年,在全球18種主要船型中,我國共有12種船型新接訂單位列世界第一。其中,新接散貨船、集裝箱船、汽車運輸船和原油船訂單分別占全球總量的74.3%、56.8%、88.7%和66.1%。
造老船、走老路行不通,轉換賽道才能滿盤皆活
中國船舶集團江南造船公司(以下稱“江南造船”)擁有158年悠久歷史,由其建造的“中國江南型”巴拿馬散貨船是中國第一個在國際租船市場上掛牌交易的著名品牌。11年前,散貨船行情興旺,已實現(xiàn)批量化生產的江南造船不愁“接單”,卻作出了一個“意外”決定——暫停承接散貨船新訂單,把重心放在高技術復雜船型的研發(fā)上。
居安思危。“散貨船技術門檻低,競爭激烈,我們無法通過做更多散貨船來提升企業(yè)的盈利水平。液化天然氣船(LNG)等技術難度高、新型環(huán)保船舶的市場需求穩(wěn)步提升,利潤空間更大,是一片前景廣闊的‘藍海’。江南造船瞄準液化氣船這一細分市場,研發(fā)建造超大型液化石油氣船(VLGC)和超大型乙烷運輸船(VLEC)。”江南造船研究院院長助理、開發(fā)研究所所長,VLEC副總工藝師周清華說。
轉型并非一蹴而就。“江南造船目前擁有全球最大的VLEC市場份額,VLEC技術經濟性能指標處于國際領先水平。從跟跑到領跑,我們用了整整8年時間。”周清華說。
VLEC的關鍵技術難點在于貨物圍護系統(tǒng)的研發(fā)建造。這也是氣體船研制的核心技術,承擔著將低溫液貨圍護在一定空間內,以低蒸發(fā)率、大容積、安全為前提運達目的地的任務。周清華帶領團隊開展B型艙(一種新型液化氣圍護系統(tǒng))的總體布局、結構、絕緣、次屏壁的設計、分析和試驗等關鍵技術攻關工作,自主研發(fā)設計具有完整知識產權的“BrilliancE”型圍護系統(tǒng),申報三十余項專利,建造完成世界首艘搭載B型艙的9.9萬立方米超大型乙烷運輸船。
通過自主創(chuàng)新向中高端市場轉型,是成為世界一流造船企業(yè)的必經之路。就在江南造船深耕大型液化氣船時,廣船國際把目光投向了汽車運輸船。
2018年,廣船國際完成產能從廣州市區(qū)到龍穴造船廠區(qū)的轉移搬遷。“當時造船條件比較落后,我們詳細研究后得出結論:造老船、走老路行不通了,轉換賽道才能滿盤皆活。”周旭輝說。
危中求機。2020年,我國汽車出口108.2萬輛;2021年,達到201.5萬輛……廣船國際從汽車出口數(shù)據(jù)中尋覓到了商機。
“看到了汽車特別是新能源汽車產業(yè)的變化,我們就琢磨自己該怎么應變。”周旭輝說,汽車出口量增長帶動汽車運輸船需求和價格“水漲船高”,因此公司加大投入,轉入汽車運輸船賽道。
汽車運輸船屬于船舶市場中相對小眾的特種運輸船,過去我國造船企業(yè)涉足較少。抓住這一機遇,廣船國際攻克了薄板變形控制、船體結構精度控制、滾裝設備安裝調試以及LNG雙燃料推進系統(tǒng)等關鍵核心技術,打造海上巨型“立體車庫”,目前汽車運輸船手持訂單數(shù)量世界領先。今年9月,廣船國際聯(lián)合中船貿易建造的7000車LNG雙燃料汽車運輸船“埃姆登”號正式交付給挪威SFL公司,這是華南地區(qū)建造的首艘雙燃料汽車運輸船。10月24日,該船型的4號船已順利出塢。
綠色化、智能化改變造船業(yè)面貌
新能源汽車受歡迎,新能源船舶同樣是國際市場上的“香餑餑”。在P&O1500客/3658米車道豪華客滾船2號船上有4個電池間,共配備1160塊大容量電池,電池裝船容量達到8.8MWh(兆瓦時),相當于150輛乘用電動汽車的電池容量之和。
“燃油發(fā)電推進模式和電池推進模式可實現(xiàn)一鍵切換,并在進出港作業(yè)及近海航行時采用純電力推進,從而實現(xiàn)污染物‘零排放’,減少對港口和城市的空氣污染。”廖明說。
2022年,我國全年新接綠色動力船舶訂單占總訂單的49.1%,創(chuàng)歷史最高水平。“目前公司手持造船訂單中有近40艘、價值200億元的訂單為高附加值的甲醇雙燃料或LNG雙燃料新型綠色船型。”周旭輝說。
綠色低碳,正是我國船舶工業(yè)轉型升級的發(fā)力點。2018年4月,國際海事組織(IMO)通過了全球首份航運業(yè)溫室氣體減排初步戰(zhàn)略“海運減排協(xié)議”,制定了2050年航運業(yè)的年度溫室氣體排放總量相比2008年減少50%的目標,并主張在全球范圍內加速推動船舶新能源和替代能源的應用。2022年9月,我國工信部、國家發(fā)展改革委等五部委聯(lián)合公布的《關于加快內河船舶綠色智能發(fā)展的實施意見》指出,積極穩(wěn)妥發(fā)展LNG動力船舶、加快發(fā)展電池動力船舶。
使用液化天然氣作為動力已成趨勢,甲醇、氫氣、氨等綠色燃料作為動力的船舶也在研發(fā)之中,而綠色船舶不僅體現(xiàn)在船舶動力的選擇上,還體現(xiàn)在船舶設計建造的各方面。
“以研發(fā)源頭控碳為例,我們從減阻技術、船型開發(fā)技術以及低碳處理技術等方面出發(fā),深耕綠色低碳智能船型研發(fā)。”周清華說,船舶的輕量化設計、新型節(jié)能環(huán)保材料的應用、提高材料利用率等措施,都能從設計源頭降低船舶建造的碳排放量,降低總裝造船業(yè)務的碳排放。
數(shù)字化制造、智能化裝備廣泛應用,也改變著我國造船業(yè)的面貌。在江南造船的數(shù)字化展廳,戴上3D眼鏡便如同置身于一艘高度仿真的“數(shù)字船”,將船艙內的情況盡收眼底。
“借助數(shù)字化創(chuàng)造的‘虛實結合’體驗,設計師可以對整條船的性能、工藝進行全面審視,比如驗證各艙室的溫度、聲音、光照、氣流等是否舒適宜人,或者‘駕駛’吊車等裝備進入‘數(shù)字船’,檢查船舶在檢修時能否使用大型工具和工裝,準確評估維修路徑的可行性等。”周清華介紹,數(shù)字化工具就像庖丁解牛,把船舶這個巨系統(tǒng)拆解得清清楚楚,整合得天衣無縫,從而提升設計、制造的效率。目前,江南造船大型液化氣船的設計建造已實現(xiàn)全系列數(shù)字化,設計周期縮短,產品的市場競爭力顯著增強。
發(fā)展產業(yè)集群并完善配套供應鏈是未來努力的方向
“我們從2001年開始建造客滾船,走過不少彎路。”周旭輝說。
2014年,船型相似的客滾船,廣船國際簽下的訂單價格為1.79億美元;在此之前,一位國際同行簽下的訂單價格為0.79億美元。“雖然船的配置不同,且有船價上漲等因素,但我心想畢竟多了1個億,我們肯定會盈利。結果船造出來,一算還虧本了。”痛定思痛后,周旭輝和同事們找到了問題的根源。
一艘船背后,是一條超長供應鏈。
“一個是價格問題,當時國產供應鏈尚未到位,很難達到國外同類產品的質量標準,多數(shù)材料、設備只能按照船東要求進口,利潤率被壓低;一個是履約問題,國外設計和進口時間長、不可控因素多,影響船舶交付周期,導致成本居高不下。”周旭輝說。
由于涉及工業(yè)品類多,建造技術工藝復雜,造船業(yè)被譽為“綜合工業(yè)之冠”。近年來,中國制造實力穩(wěn)步提升,中國造船企業(yè)持續(xù)培育國內船舶產業(yè)上下游供應鏈,推進配套設備和資材的國產化,并聯(lián)合科研院所合力突破關鍵領域的“卡脖子”難題。
廣船國際聯(lián)合相關設計院所就豪華客滾船設計開展密切合作,成功孵化并帶動了減搖鰭、軸帶發(fā)電機、廢熱透平發(fā)電機組等領域的一大批國內配套企業(yè)進入國際高端豪華客滾船市場;推進艙室內裝國產化,通過建造艙室樣板間、帶領船東考察國內供應商等辦法,以過硬的產品品質贏得船東信任。
“20多年前,由廣船國際建造的國內首艘豪華客滾船內裝材料幾乎全部進口?,F(xiàn)在,我們聯(lián)合國內上下游供應商建立起完整的產業(yè)鏈,實現(xiàn)豪華客滾船內裝設計、采購、施工全流程的100%國產化。”周旭輝說,實現(xiàn)產業(yè)鏈國產化后,客滾船建造周期大幅縮短,“以前兩三年完工一艘船,現(xiàn)在一年完工多艘船”。
“國內郵輪產業(yè)鏈正在成長。大型郵輪開建以來,上海已經新增注冊了許多郵輪內裝公司和船東運營公司,既有國內的也有外資的,這是郵輪產業(yè)帶動效應的體現(xiàn)。”據(jù)外高橋造船開發(fā)部總體開發(fā)室主任黃毅銘介紹,外高橋造船還成立了大型郵輪創(chuàng)新中心,促進上下游產業(yè)鏈建設,目前已有40余家優(yōu)勢企業(yè)入駐。
國產首艘大型郵輪計劃于明年初從上海吳淞口國際郵輪港啟航。“創(chuàng)新無止境,發(fā)展產業(yè)集群并完善配套供應鏈是未來努力的方向。我們要把接力棒一代代傳下去,讓中國船舶工業(yè)的創(chuàng)新能力和技術實力節(jié)節(jié)躍升。”陳剛說。(本報記者 柴雅欣)
- 2023-11-07學思踐悟再出發(fā)——全省紀檢監(jiān)察宣傳業(yè)務培訓班側記
- 2023-11-07李希同越共中央政治局委員、中央書記處書記、 中央檢查委員會主任陳錦繡舉行會談
- 2023-11-07習近平會見全國“楓橋式工作法”入選單位代表 蔡奇李希參加會見
- 2023-11-01深度關注 | 從嚴整治“微腐敗”

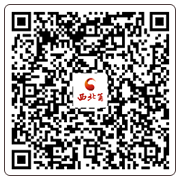
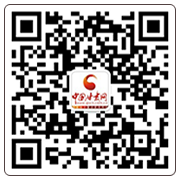
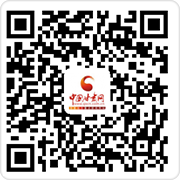
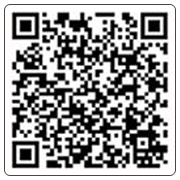
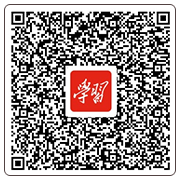
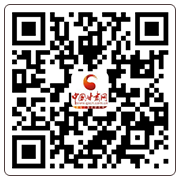